IL CICLO DI LAVORO
Il processo di verniciatura a polveri per tutti i prodotti da noi lavorati
è composto principalmente da sette fasi :
- PREPARAZIONE E CARICO
- PRETRATTAMENTO IN TUNNEL A SPRUZZO
- ASCIUGATURA CON ARIA CALDA IN FORNO
- 1° RAFFREDDAMENTO NATURALE ALL’ ARIA
- VERNICIATURA IN CABINE CON APPLICAZIONE DI POLVERI
- COTTURA/POLIMERIZZAZIONE POLVERI CON ARIA CALDA IN FORNO
- SCARICO DEI PARTICOLARI DAL TRASPORTATORE AEREO CON IMBALLAGGIO E CONFEZIONAMENTO SECONDO LE ESIGENZE
PREPARAZIONE E CARICO
– Preparazione dei prodotti da verniciare e divisione degli stessi per tipologia, dimensione e per tipo di finitura;
– Carico dei pezzi sulla linea;
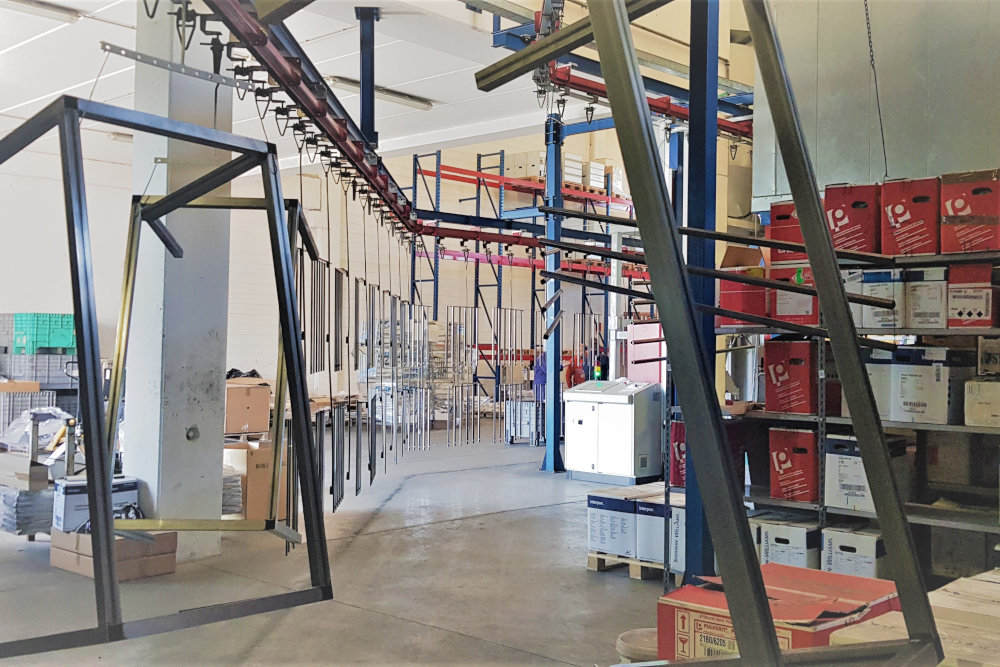
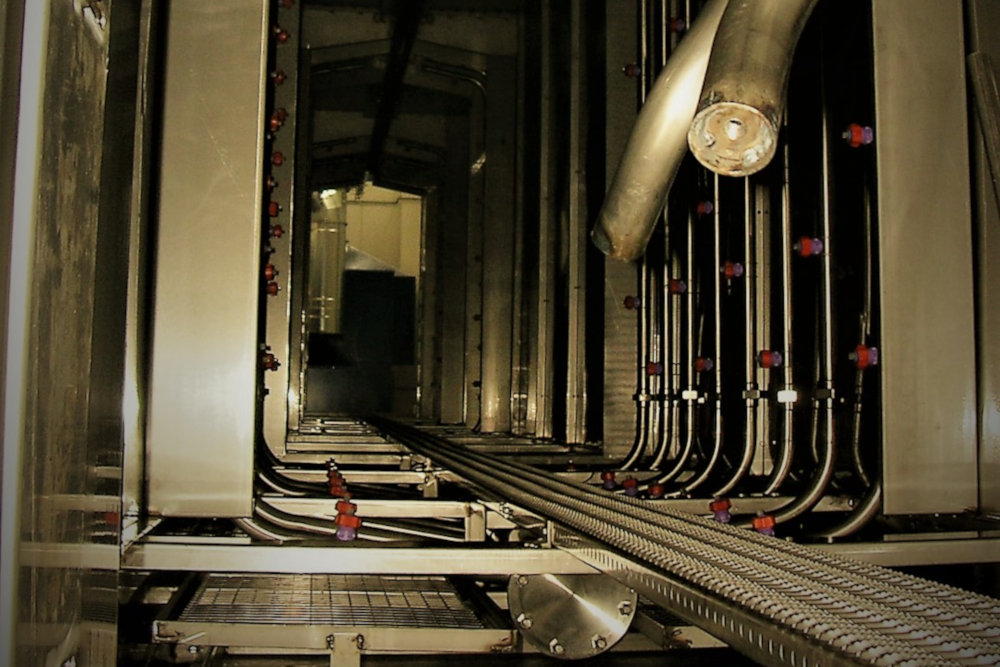
PRETRATTAMENTO IN TUNNEL A SPRUZZO
Dopo essere stati caricati sulla linea, i pezzi sono diretti al tunnel di pretrattamento, il quale è composto da 4 fasi distinte:
- fosfosgrassaggio;
- risciacquo acqua di rete;
- risciacquo acqua di rete;
- risciacquo con impianto demi;
La prima fase è denominata fosfosgrassaggio, ossia una conversione superficiale dei particolari che elimina le impurità derivanti da lavorazioni precedenti, attraverso una soluzione nanotecnologica e allo stesso tempo prepara i supporti alla successiva . Questo lavaggio viene effettuato ad una temperatura di circa 50 °C con un PH di soluzione che varia dai 4,5 ai 6 punti, dato che viene costantemente monitorato da un dosatore automatico il quale dosa i detergenti in base al necessario, in modo tale da ridurre al minimo il quantitativo di soluzioni di lavaggio utilizzate in produzione;
Il successivo stadio di pretrattamento viene effettuato da un primo risciacquo con acqua di rete a temperatura ambiente atto ad eliminare le soluzioni ed i contaminanti presenti nella prima fase e da un secondo che elimina i residui del primo risciacquo, in modo tale da avere i pezzi perfettamente esenti da soluzioni che contrastino con le successive fasi della produzione;
Nell’ ultima parte del tunnel viene effettuato un nuovo risciacquo con acqua demineralizzata, in tal modo si eliminano i residui di calcare e si attiva effettivamente la superficie per la successiva verniciatura.
Inoltre possiamo far notare che questo processo è totalmente a ciclo chiuso, del tutto in linea con le vigenti normative di sicurezza ambientale, in quanto non vi è assolutamente fuoriuscita di acque di processo durante le lavorazioni poichè vengono trattate con impianti idonei, durante il ciclo di lavoro. Ciclicamente i bagni di lavaggio vengono rinnovati e smaltiti da ditte preposte al ritiro ed allo smaltimento, ponendo sempre attenzione alla salvaguardia ambientale.
Scarico Zero
“Quando l’acqua, dopo essere stata utilizzata, viene restituita al suo ambiente naturale, non deve comprometterne i possibili usi, tanto pubblici che privati. La sua salvaguardia implica un notevole sforzo di ricerca scientifica, di formazione di specialisti e di educazione del pubblico.”
Ricordando i rischi di siccità che hanno colpito e potranno colpire l’Italia e l’Europa, possiamo renderci conto di quanto sia importante risparmiare e ridurre i consumi di acqua, recuperandola e riutilizzandola in ogni possibile situazione. Un’attenta e moderna progettazione degli impianti di lavorazione e dei cicli di processo con l’utilizzo di lavaggi in cascata, permette di ottimizzare i consumi di acqua e di inserire macchine, impianti e sistemi depurativi che, basandosi su concetti tecnologici diversi ed innovativi, consentono la depurazione dei reflui e spesso anche il loro recupero e riutilizzo.
Conseguenza di tutto questo è un doppio risparmio, che si può rivelare come un vero e proprio guadagno in termini economici, dato dalla duplice possibilità di:
- recuperare completamente l’acqua dai reflui inquinati (scarico zero) ed utilizzarla per rabboccare e/o reintegrare i bagni di lavorazione;
- ridurre al minimo il quantitativo d’ inquinante da conferire alle aziende autorizzate per lo smaltimento o, in alcuni casi, di renderne possibile il riutilizzo all’interno del bagno stesso di lavorazione.
- ridurre l’impatto ambientale
ASCIUGATURA
Al termine della fase di pretrattamento segue l’asciugatura in un tunnel per la durata di 18 minuti e ad una temperatura media di 130 °C. In questa fase la gestione della temperatura è molto importante, in quanto se troppo elevata, va a distruggere lo strato creato in precedenza dal pretrattamento, riducendo così l’adesione del prodotto verniciante.
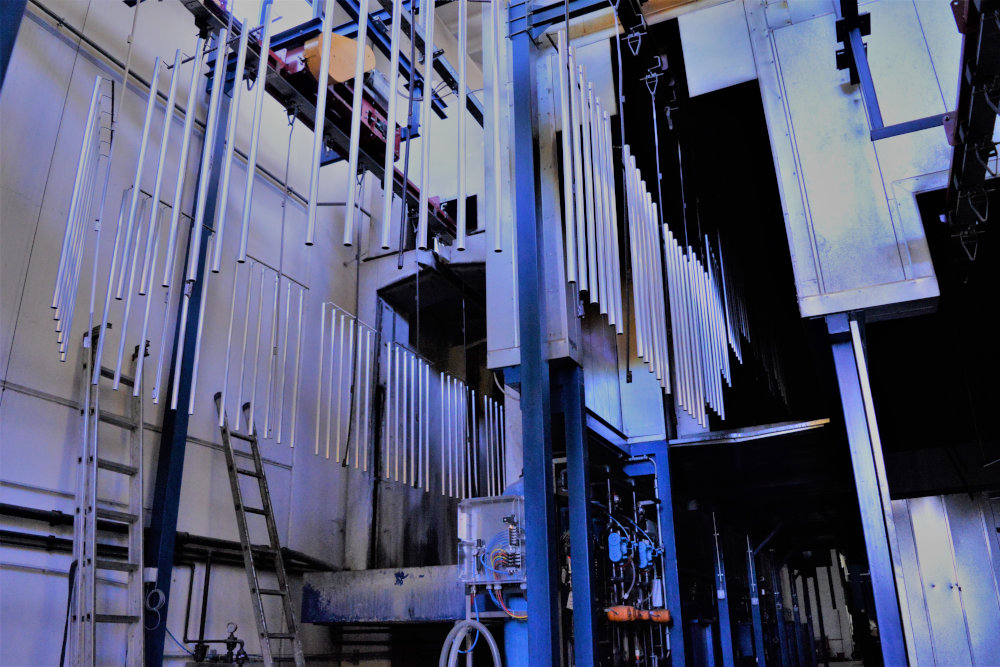
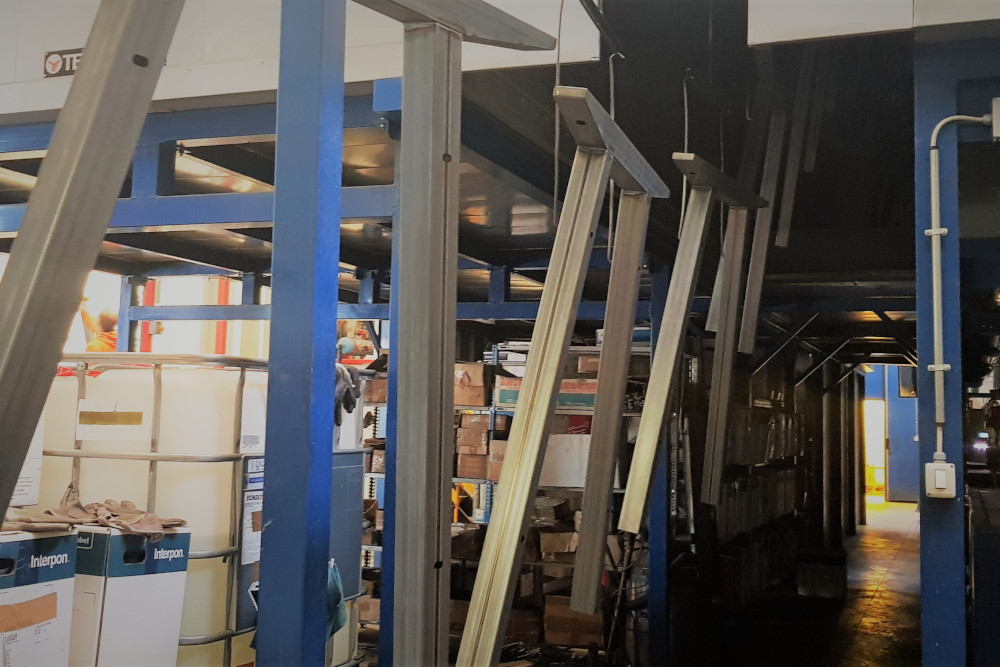
1° RAFFREDDAMENTO
Il raffreddamento dei pezzi è determinato dal tempo che trascorre tra l’uscita dal forno e l’ entrata nelle cabine di verniciatura. Generalmente l’ impianto lavora in ciclo continuo, quindi il tempo di raffreddamento corrisponde al tempo impiegato dal pezzo per attraversare la distanza tra le due zone che, a sua volta, dipende dalla velocità del trasportatore. Questa fase è molto importante per il ciclo, perché ha lo scopo di impedire che la vernice si ritragga durante la fase di applicazione, evitando così che l’ intero lotto venga rifiutato.
APPLICAZIONE POLVERI
Al fine di evitare eventuali contaminazioni tra i diversi colori utilizzati nel ciclo di verniciatura l’impianto di verniciatura è dotato di 3 cabine in linea distinte, per l’applicazione dei vari colori:
- CABINA N°1 – TINTE SCURE
- CABINA N°2 – TINTE CHIARE
- CABINA N°3 – PICCOLI LOTTI E FINITURE AD EFFETTO
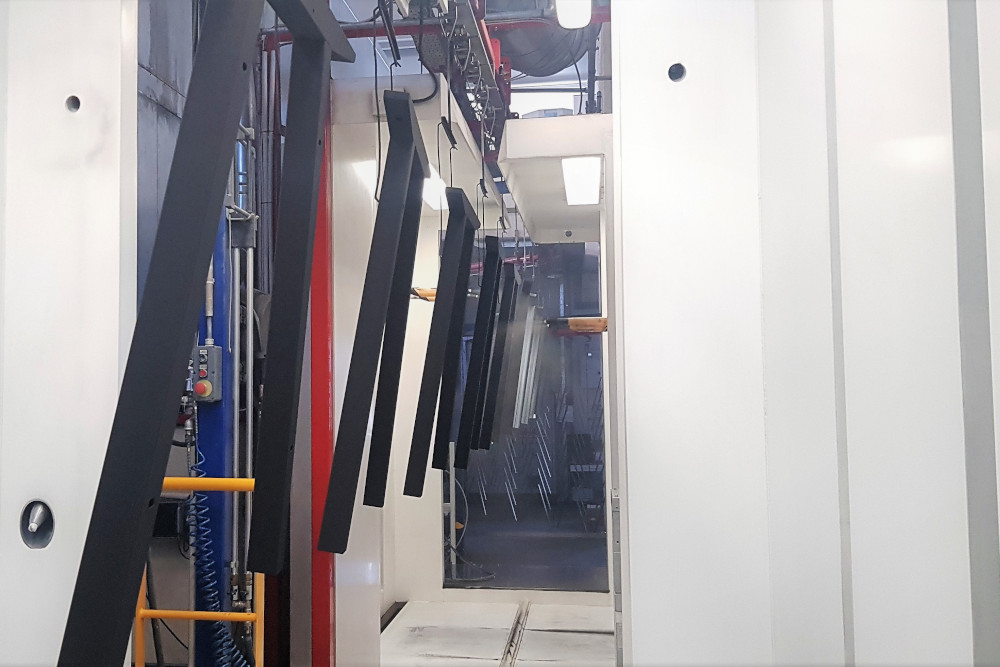
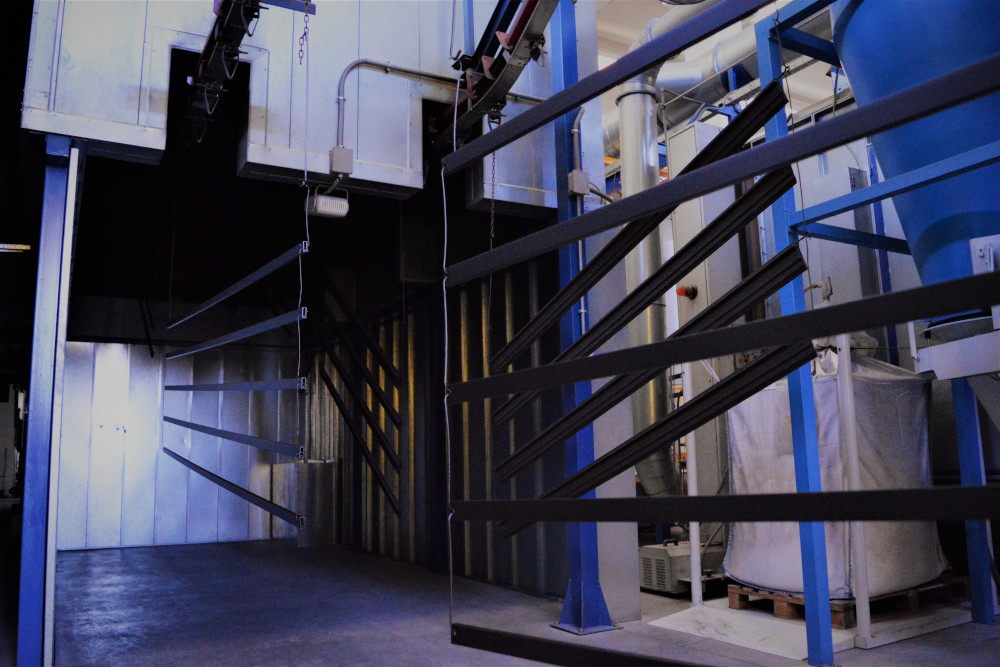
POLIMERIZZAZIONE
Questa è la fase del ciclo di verniciatura in cui la vernice in polvere “cuoce” (reticola), all’interno del forno di essiccazione ad una temperatura media di esercizio di circa 190 °C per un tempo medio di 35 minuti; il tempo e la temperatura varia a seconda dei materiali da trattare, infatti i pezzi in fase di preparazione vengono suddivisi in base alle geometrie e tipologie perché ogni materiale ha proprie caratteristiche di conducibilità termica, in quanto è la temperatura del pezzo a permettere l’inizio della reazione di polimerizzazione del prodotto verniciante.
SCARICO
Questa è la fase finale del ciclo di verniciatura e consiste nello scaricare i pezzi verniciati dal trasportatore e stoccarli in contenitori appositi nell’attesa dell’eventuale imballaggio degli stessi nelle rispettive scatole. La scelta dell’imballaggio per ogni singolo pezzo verniciato viene fatta insieme al cliente al momento della richiesta dell’ordine.
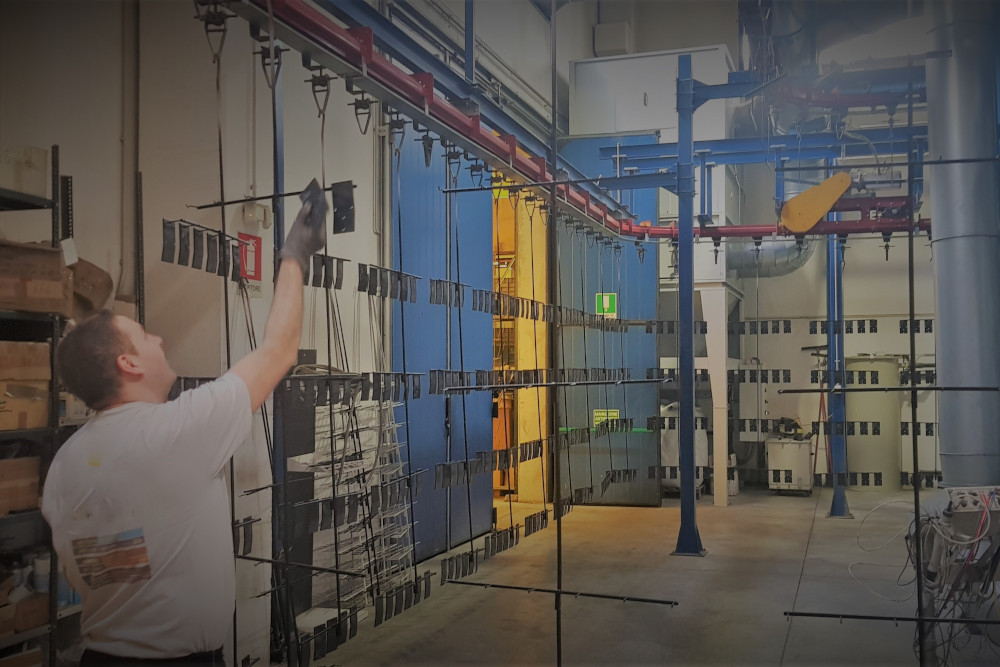